
IQMS: Integrated Quality Management System
Integrated level 2 factory system, allows data collection and supervision of all activities carried out at both Level 3 and Level 1 in the production lines, a single system to keep under control everything needed to guarantee the quality of a product in the following areas.
- Pre-assembly
- Assembly
- Shipping
The production database server is a collector of all the information flowing from and to the production and, in support of an application-server, supervises all the assigned control stations, verifying compliance with the rules envisaged during the setup phase.
The historical database server contains all the information necessary for the certification and reporting of the history of a factory both in terms of productivity and quality, allowing the subsequent verification of tests carried out on each product sold on the market.
Menus that can be tailored according to the user and the Client workstation used. Multilingual management through a special interface, change on the fly of the current language.
Management of the master data of all the main activities such as system users, descriptions of defects etc.
Documentation (Jpg / Pdf): in the coding of the articles, possibility of associating images and photos (Jpg) or documents (Pdf).
Interfaces to the supervision stations of the production lines / laboratories through network connections using OPC, database and / or exchange through XML in the simplest cases.
System expandability, given by the possibility of adding new stations to those already present without any limit to the quantity. This approach allows you to start with a "minimal" system and expand it at a later time without affecting any functionality other than upgrading the hardware if deemed necessary.
Definition of all the data necessary for the production process to be classified for each new item such as project, energy and environmental certifications.
Assignment of the rules for the approval of the data flow, rules that define the reliability of the data and any responsibilities of those who introduce it.
Definition of the labels that must be integrated into the finished product such as Energy, Rating Plate, Warranty, Packaging etc through a special graphic editor with integrated tools for the dynamic printing of process information.
Automatic generation of serial numbers with online control and blocking of any duplicates.
Definition of the line stations according to the type of data required:
Production counting and payment stations
Test stations with interfaces to the instrumentation used online for the collection of test data
Traceability and control stations for critical components with verification of the correct associations declared in BOM
Definition of working calendars and shifts divided by production line.
Production efficiency report on the stations under control.
Synoptic of the interfaced production lines with visualization of the stations under control in terms of tests and defects found.
Verification through the assigned line stations of compliance with the rules defined in the system setup.
Online updating of all production information such as partial counts, per shift, per station etc.
Online update of productivity efficiency calculation (often used for the distribution of production bonuses)
User interface for programming the quality rules for each line station such as number of tests and compliance with the sequence before authorizing the shipment of a product to the warehouse.
Verification online per station of compliance with the scheduled rules.
Authorization for each station to perform tests after verification of safety conditions, for example avoiding that an electrical test is carried out without having first verified the earth test and so on.
Check that a product does not go into stock before it has been repaired.
Calculation of the quality index per shift using real-time information from line repairers.
Repair stations with display of the problem encountered and classification of the real defect through a special registry managed by the quality.
Traceability of critical components with the option of verification and acceptance in derogation during the assembly phase.
Statistics and efficiency indicators, the system allows the complete consultation of all the production statistics being able to rely on a database in which all the information collected is historicized, allowing the capillary analysis of all the substantial data defined by the system (KPI, OEE) and by the user, analyzing the individual phases of interest
Procedure for statistical quality verification for each production batch with automatic calculation of the batch index.
Automatism for sending or reporting the products to be checked during the production process according to rules defined during the system setup.
Procedure for the management of both destructive and non-destructive testing laboratory.
Using all modern tools it is possible to define the types of tests to be subjected to the product, the system will supervise the test by generating scheduled events to guide the operator during all phases of the various checks.
It will be possible to archive photos or documents that will be historicized for subsequent historical analysis.
Any event of any type can be scheduled to send emails or reports on any tool connected to the internet.
Given the amount of data collected, both productive and qualitative basic reports are provided and it is also possible to implement others based on specific needs.
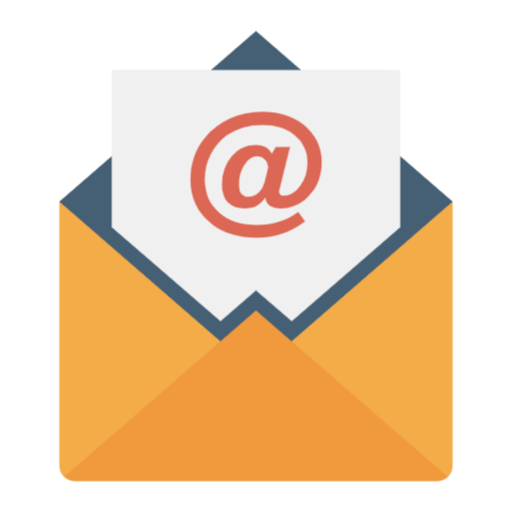
mail: info@itacasw.it
Phone: +39 0734.445279
Do you want to request more information or book a free demo?